Vulcanization stands as a cornerstone process in rubber manufacturing, crucial for transforming raw rubber into durable, usable products. Among the various techniques employed, vacuum vulcanization emerges as a specialized method with distinct advantages and characteristics, setting it apart from conventional vulcanization approaches. Understanding the key differences between
Vacuum Rubber Vulcanizing Machine and other methods is paramount for manufacturers seeking to optimize their production processes and achieve superior quality rubber goods.
Pressure Environment:
Vacuum Vulcanization: This method operates in a controlled vacuum environment, wherein air pressure is reduced below atmospheric levels. By removing air and trapped gases from the rubber material and mold cavity, vacuum vulcanization minimizes the formation of voids and air bubbles, leading to denser and more uniform products.
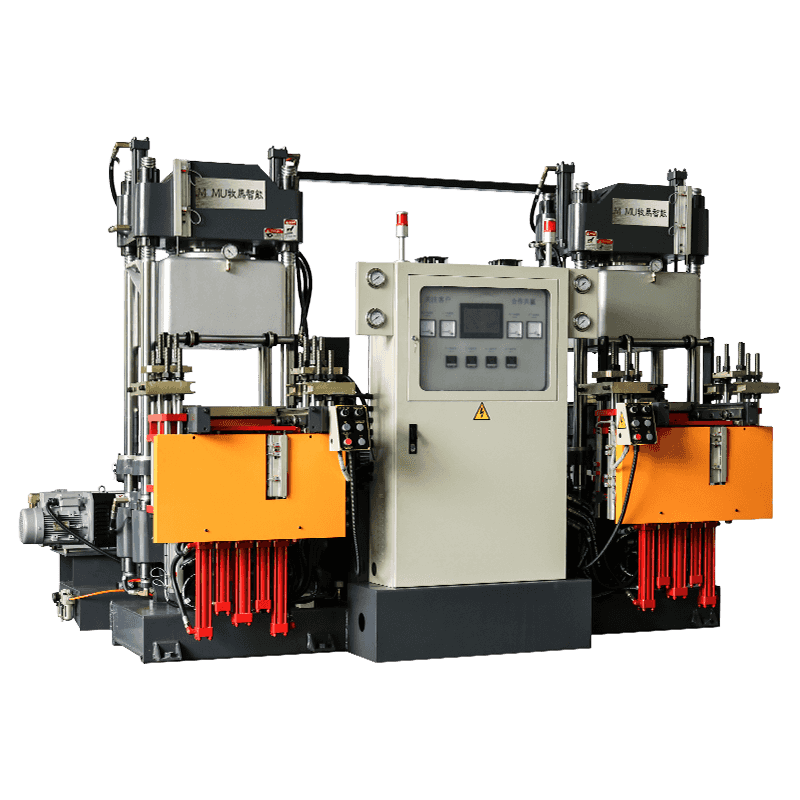
Other Vulcanization Methods: Conventional vulcanization techniques, such as compression molding or injection molding, typically occur either at atmospheric pressure or under high pressure. While effective, these methods may not offer the same level of air removal and control as vacuum vulcanization, potentially resulting in inconsistencies in the final product.
Air Removal:
Vacuum Vulcanization: Integral to the process is the thorough evacuation of air from both the rubber material and the mold cavity. This step ensures that the rubber is free from trapped air pockets, which can compromise the structural integrity and surface finish of the finished product.
Other Vulcanization Methods: While air removal is also essential in other vulcanization methods, it may not be as rigorously controlled as in vacuum vulcanization. Consequently, these methods may be more susceptible to the formation of air voids within the rubber, affecting its quality and performance.
Enhanced Material Properties:
Vacuum Vulcanization: By eliminating air pockets and ensuring uniform material density, vacuum vulcanization yields rubber products with enhanced material properties. These may include improved tensile strength, tear resistance, and surface finish, making them ideal for applications demanding high-performance rubber components.
Other Vulcanization Methods: While capable of producing quality rubber products, conventional methods may not achieve the same level of material consistency and integrity as vacuum vulcanization. This can impact the durability and reliability of the end products, particularly in demanding or critical applications.
Mold Design and Complexity:
Vacuum Vulcanization: The specialized nature of vacuum vulcanization often necessitates the use of custom molds designed to withstand vacuum pressure and facilitate efficient air evacuation. These molds may exhibit greater complexity compared to those used in other vulcanization methods.
Other Vulcanization Methods: Depending on the specific process and product requirements, conventional vulcanization methods may employ simpler molds or tooling designs. While less intricate, these molds remain effective for their intended purposes but may lack the sophistication required for vacuum vulcanization.
Production Speed and Efficiency:
Vacuum Vulcanization: Due to the meticulous air removal process and controlled curing conditions, vacuum vulcanization may entail longer curing times compared to other vulcanization methods. However, the resulting rubber products often exhibit superior material quality and consistency.
Other Vulcanization Methods: Conventional methods, such as injection molding, may offer faster production cycles but could sacrifice some degree of material quality and uniformity. The choice between speed and quality depends on the specific manufacturing requirements and desired end-product characteristics.