When it comes to producing high-quality insulators for electrical applications, injection molding technology has been a game-changer. This innovative manufacturing process has revolutionized the way insulators are produced, offering improved efficiency, precision, and cost-effectiveness. In this article, we will explore the latest advancements in injection molding machines for insulators and how they are shaping the future of this essential component in electrical systems.
One of the key developments in insulator injection molding technology is the integration of advanced materials. With the increasing demand for insulators that can withstand extreme weather conditions and high voltage applications, manufacturers are turning to materials such as silicone rubber and composite polymers. These materials offer superior insulation properties and durability, making them ideal for a wide range of electrical infrastructure projects. Injection molding machines equipped to handle these advanced materials are enabling the production of insulators that meet the most stringent industry standards.
In addition to material advancements, the latest
insulator injection molding machines are equipped with cutting-edge automation and control systems. These systems allow for precise monitoring and adjustment of the injection molding process, ensuring consistent quality and dimensional accuracy of the insulators. Furthermore, the integration of robotics and artificial intelligence in injection molding technology has significantly enhanced production efficiency and reduced the risk of defects. As a result, manufacturers can meet the growing demand for insulators with improved productivity and reliability.
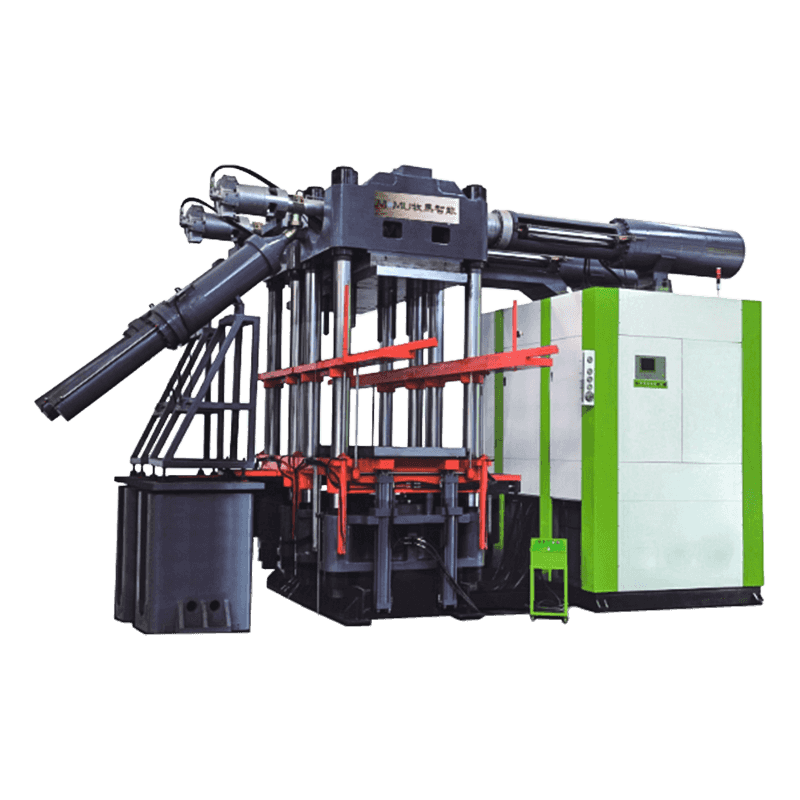
Furthermore, sustainability has become a major focus in the development of insulator injection molding machines. With the increasing pressure to reduce environmental impact, manufacturers are actively seeking ways to minimize material waste and energy consumption in the production process. Modern injection molding machines are designed to optimize material usage and energy efficiency, contributing to a more sustainable manufacturing approach. Additionally, the use of biodegradable and recyclable materials in insulator production has gained traction, aligning with the industry’s commitment to environmental responsibility.
The evolution of insulator injection molding machines is driving significant advancements in the production of high-performance insulators for electrical applications. From advanced materials to automation and sustainability, these technological innovations are reshaping the industry and setting new standards for insulator quality, reliability, and environmental responsibility. As the demand for efficient and durable insulators continues to grow, the ongoing development of injection molding technology holds great promise for the future of electrical infrastructure worldwide.