Material Inspection:
Raw material inspection is performed to ensure that the rubber compounds used in the molding process meet the required specifications in terms of composition, consistency, and quality.
Preheating and Temperature Control:
Proper preheating of the mold and precise temperature control of the molding process are crucial for achieving consistent and high-quality parts.
Temperature sensors and controllers are used to monitor and control the temperature of both the mold and the rubber material during the molding process.
Pressure Control:
Control of the molding pressure is critical for achieving proper material flow and ensuring the desired part density and dimensions.
Pressure sensors and hydraulic systems are used to regulate and maintain the compression pressure applied during the molding process.
Cycle Time Monitoring:
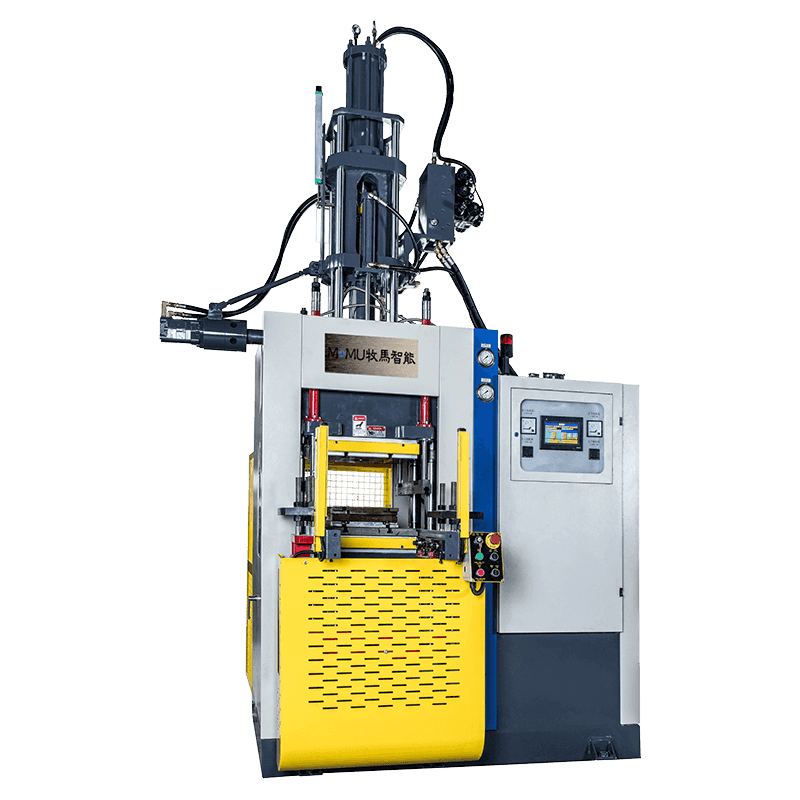
Monitoring the cycle time of the molding process ensures that the production runs efficiently and consistently.
Any deviations from the standard cycle time may indicate issues with the equipment or process that need to be addressed.
Visual Inspection:
Visual inspection of the molded parts is performed to detect any defects such as surface imperfections, air traps, flash, or incomplete filling.
Quality control personnel visually inspect the parts to ensure they meet the required aesthetic and dimensional standards.
Dimensional Inspection:
Dimensional inspection is carried out using measuring instruments such as calipers, micrometers, and gauges to verify that the molded parts meet the specified dimensions and tolerances.
Testing and Quality Assurance:
Quality assurance procedures may include conducting various tests on the molded parts to assess their mechanical properties, such as tensile strength, elongation, hardness, and compression set.
Samples may be subjected to destructive or non-destructive testing methods to ensure they meet the required performance criteria.
Traceability and Documentation:
Maintaining proper documentation throughout the manufacturing process, including batch records and quality inspection reports, ensures traceability and facilitates identification of any issues or deviations.By implementing these quality control measures, manufacturers can ensure consistent production of high-quality rubber molded parts that meet the required specifications and standards.