Daily Maintenance:
Clean the mold surfaces and remove any debris or residue.
Check and lubricate moving parts such as guide rails, hinges, and hydraulic cylinders.Inspect safety features such as emergency stop buttons and interlocks to ensure they are functioning correctly.
Check hydraulic fluid levels and top up if necessary.
Inspect electrical components for any signs of wear or damage.
Weekly Maintenance:
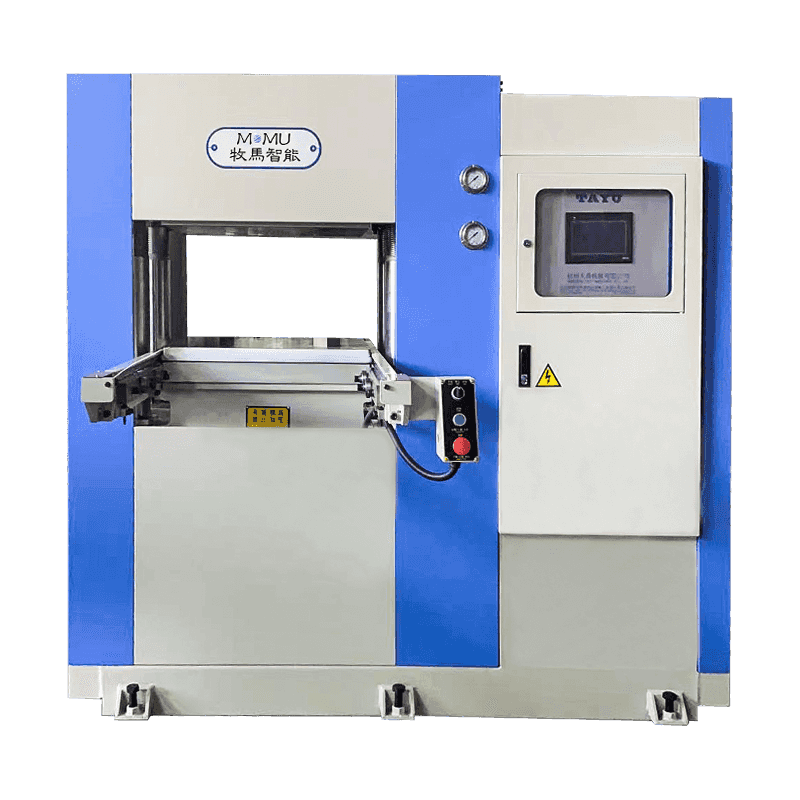
Perform a more thorough inspection of the mold components, including seals, heating elements, and cooling channels.Clean and inspect the hydraulic system, including filters and hoses, and replace any worn or damaged parts.Check the alignment of the mold and platens to ensure they are parallel and properly aligned.
Verify the accuracy of temperature and pressure sensors/controllers.
Monthly Maintenance:
Inspect and clean the heating and cooling systems, including heaters, thermocouples, and water lines.Check the condition of mold release agents and replace if necessary.Calibrate temperature and pressure sensors/controllers as needed.Perform a thorough inspection of all safety features and emergency systems.
Quarterly Maintenance:
Inspect and clean the entire machine, including the frame, platens, and control panels.Lubricate all bearings and moving parts according to the manufacturer's recommendations.Check the condition of electrical wiring and connections, and tighten or replace any loose or damaged components.Test the functionality of all control systems and safety features.
Annual Maintenance:
Perform a comprehensive inspection of all major components, including the hydraulic system, electrical system, and mechanical components.Replace worn or damaged parts as needed, including seals, hoses, and hydraulic cylinders.Grease or replace bearings as necessary.
Conduct a thorough cleaning of the entire machine and perform any necessary adjustments or alignments.
Training and Documentation:
Ensure that maintenance personnel are properly trained in the operation and maintenance of the compression molding machine.
Keep detailed records of all maintenance activities, including inspections, repairs, and replacements.
By following a regular maintenance schedule and performing routine inspections, manufacturers can minimize downtime, reduce the risk of unexpected failures, and prolong the life of their rubber compression molding machines.